Sealed Bearing Packs & Motors
The Rapid sealed bearing pack was specifically engineered for the challenging milling operations happening in today’s industry. The Rapid sealed bearing utilizes a simple, easy to service and extremely rugged design able to withstand the harmonics of the most aggressive extended reach tools. The 50% reduction of an overall pressure drop allows more surface horsepower for drilling and cleaning the well. The Rapid motor is the next generation of sealed bearing packs
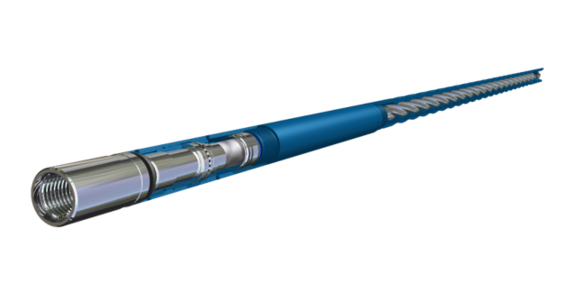
-
Engineered to be compatible with underbalanced milling
-
Rugged thread geometry to handle heavy vibration for extended periods of time
-
Titanium flex shaft
-
Stress relief housings incorporated into the design
-
Piston anti-rotation technology in bearing pack
-
Simple to service
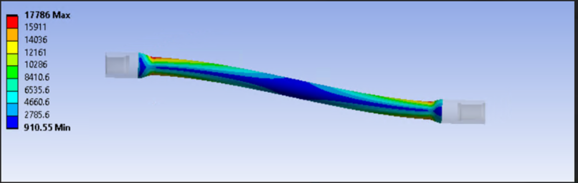
Why is Cyclical Fatigue Such a Problem in Milling
Cyclical fatigue is a problem in milling because the repetitive loading and unloading of the drill bit can cause small cracks to form in the metal, weakening it over time. This can lead to sudden and catastrophic failure of milling tools. Additionally, fatigue can cause a decrease in milling efficiency and a shorter lifespan for the tools, leading to increased maintenance costs and downtime.
Why Use BHA Placement Software
Rapid uses bottom hole assembly placement software to optimize the performance of their operations. This software allows engineers to model the drilling process, and the behavior of the drilling fluids and the materials being drilled. By using software, Rapid can select the most suitable BHA components to maximize drilling efficiency and minimize costs. Additionally, BHA placement software provides real-time data during drilling operations, allowing engineers to adjust drilling parameters and optimize drilling performance in near real-time. Overall, the use of BHA placement software helps to increase drilling efficiency, reduce costs, and ultimately maximize oil and gas production.
Why Do You Need Cumulative Damage Modelling
Rapid uses cumulative damage models to predict the degradation and eventual failure of a material or structure over time due to repeated and varying loads or stresses. These models take into account the accumulated damage caused by cyclic loading on the structure or component and provide a quantitative measure of its remaining useful life. Cumulative damage models also allow us to optimize design parameters and analyze the effects of different loading conditions on the performance of the structure.